16.2 Facility Layouts
[Author removed at request of original publisher], Published by University of Minnesota
The next step in production planning is deciding on plant layout—how equipment, machinery, and people will be arranged to make the production process as efficient as possible. In this section, we’ll examine four common types of facility layouts: process, product, cellular, and fixed position.
The process layout arranges workflow around the production process. All workers performing similar tasks are grouped together. Products pass from one workstation to another (but not necessarily to every workstation). For example, all grinding would be done in one area, all assembling in another, and all inspection in yet another. The process layout is best for firms that produce small numbers of a wide variety of products, typically using general-purpose machines that can be changed rapidly to new operations for different product designs. For example, a manufacturer of custom machinery would use a process layout.
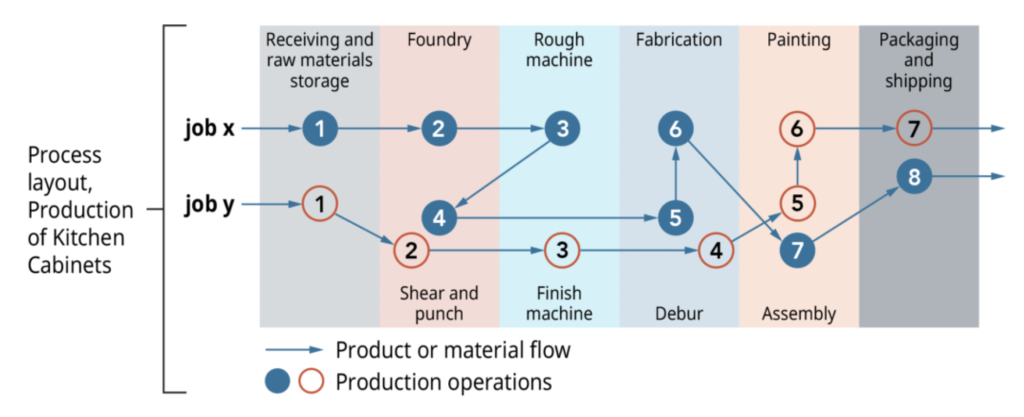
Products that require a continuous or repetitive production process use the product (or assembly-line) layout. When large quantities of a product must be processed on an ongoing basis, the workstations or departments are arranged in a line with products moving along the line. Automobile and appliance manufacturers, as well as food-processing plants, usually use a product layout. Service companies may also use a product layout for routine processing operations.
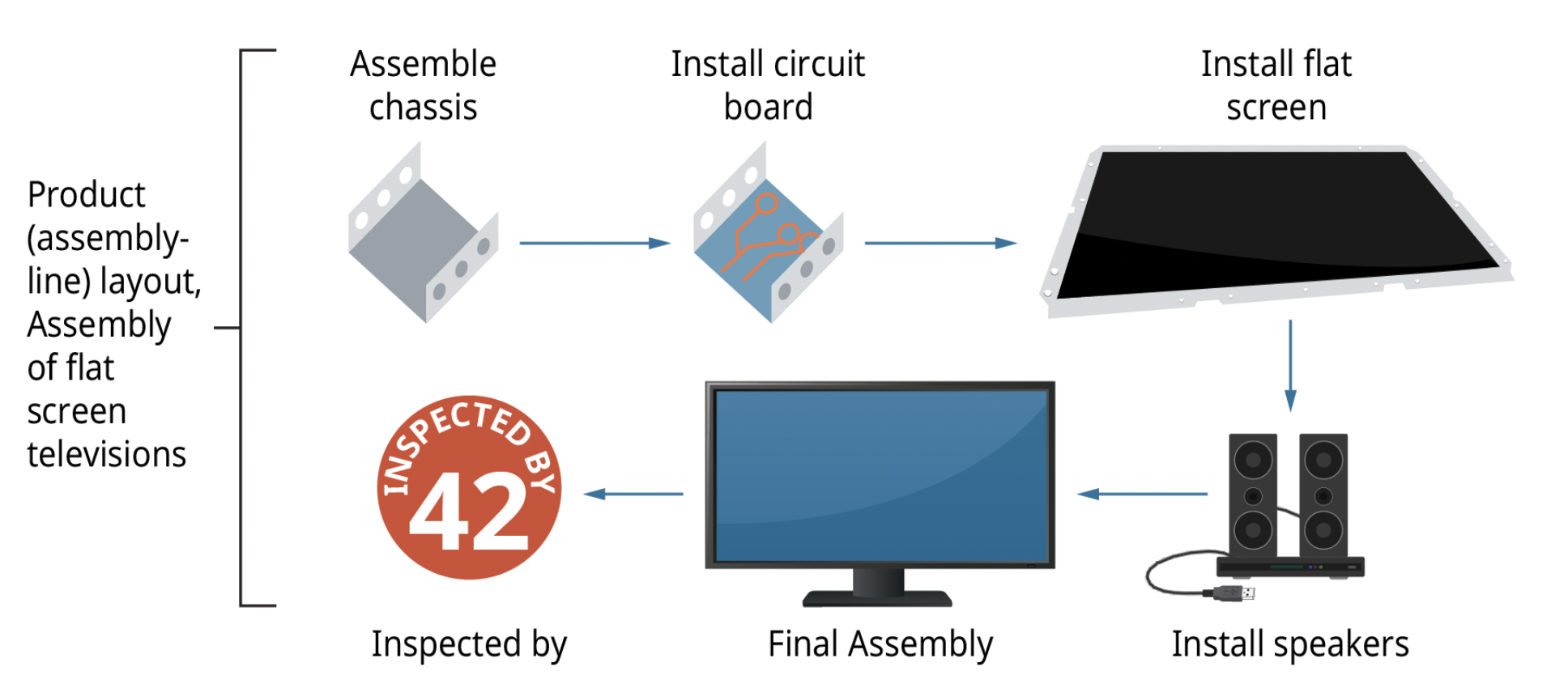
Both product and process layouts arrange work by function. At the Vermont Teddy Bear Company, for example, the cutting function is performed in one place, the stuffing-and-sewing function in another place, and the dressing function in a third place. If you’re a cutter, you cut all day; if you’re a sewer, you sew all day: that’s your function. The same is true for the production of Marshmallow Peeps at Just Born: if your function is to decorate peeps, you stand on an assembly line and decorate all day; if your function is packing, you pack all day.
Arranging work by function, however, isn’t always efficient. Production lines can back up, inventories can build up, workers can get bored with repetitive jobs, and time can be wasted in transporting goods from one workstation to another. To counter some of these problems, many manufacturers have adopted a cellular layout, in which small teams of workers handle all aspects of building a component, a “family” of components, or even a finished product. This type of layout begins with the company performing a thorough analysis of their products and deciding which products are similar to one another and often share common geometry and processing requirements in terms of equipment, machinery, technology and employee skills. These products are grouped together and manufactured in a work cell. This is referred to as group technology. Each work cell will contain a unique set of equipment to manufacture this family of parts in an assembly line type of layout. The equipment is laid out in a U shape with equipment located close together so jobs do not have to move very far.
Advantages of a cellular layout include:
1. Reduced set up times for each piece of equipment because each machine is making products that are very similar, often set-ups are very fast or non-existent.
2. Speed is greatly enhanced because batches can now be small and goods that enter the system will continue until they are complete. Small batches means fast run times and short wait times.
3. Inventory investment is now reduced due to small batch sizes enabled because of the low set up times required.
4. Quality is enhanced because employees work only within that cell on a narrow range of products. Cross training of employees ensures good and thorough knowledge of the entire production process.
5. Employee morale is improved due to working as part of a team that has responsibility for the throughput and quality of the cell. The U-shaped design heightens collaboration among workers.
6. Less floor space is required due to machines being placed close together and less movement of product.
It’s easy to move teddy bears and marshmallow candies around the factory while you’re making them, but what about airplanes or ships? In producing large items, manufacturers use fixed-position layout in which the product stays in one place and the workers (and equipment) go to the product. This is the arrangement used by General Housing Corporation in constructing modular homes. Each house is constructed at the company’s factory in Bay City, Michigan, according to the customer’s design. Because carpenters, electricians, plumbers, and others work on each building inside the climate-controlled factory, the process can’t be hindered by weather. Once it’s done, the house is transported in modules to the owner’s building site and set up in one day. For a closer view of General Housing Corporation’s production process, go to the General Housing Web site at http://www.genhouse.com.
Key Takeaways
- Managers have several production layout choices, including process, product, cellular, and fixed-position.
- The process layout groups together workers or departments that perform similar tasks. At each position, workers use specialized equipment to perform a particular step in the production process.
- In a product layout, high-volume goods are produced in assembly-line fashion—that is, a series of workstations at which already-made parts are assembled.
- In a cellular layout, small teams of workers handle all aspects of building a component, a “family of components,” or even a finished product.
- A fixed-position layout is used to make large items (such as ships or buildings) that stay in one place while workers and equipment go to the product.
Exercise
As the purchasing manager for a company that flies corporate executives around the world, you’re responsible for buying everything from airplanes to onboard snacks. You plan to visit all the plants that make the things you buy: airplanes, passenger seats, TV/DVDs that go in the back of the passenger seats, and the specially designed uniforms (with embroidered company logos) worn by the flight attendants. What type of layout should you expect to find at each facility—process, product, or fixed-position? What will each layout look like? Why is it appropriate for the company’s production process? Could any of these plants switch to a cellular layout? What would this type of layout look like? What would be its advantages?
References
Facility Location and Layout authored by Linda Williams and Lumen Learning, licensed using CC BY.
Chaneski, W., “Cellular Manufacturing Can Help You,” Modern Machine Shop, August 1, 1998, http://www.mmsonline.com/columns/cellular-manufacturing-can-help-you (accessed November 1, 2011).
Little Enterprises, Inc., http://www.littleent.com/industries.html (accessed November 2, 2011).
Modern Machine Shop Magazine, 2001, “Better Production—Manufacturing Cell Boosts Profits and Flexibility,” Modern Machine Shop Magazine, May 2001, http://www.mmsonline.com/articles/manufacturing-cell-boosts-profits-and-flexibility (accessed November 2, 2011)
how equipment, machinery, and people will be arranged to make the production process as efficient as possible
groups together workers or departments that perform similar tasks
high-volume goods are produced efficiently by people, equipment, or departments arranged in an assembly line—that is, a series of workstations at which already-made parts are assembled
small teams of workers handle all aspects of building a component, a “family” of components, or even a finished product
product stays in one place and the workers (and equipment) go to the product